QUALITY POLICY ( ISO 9001)
Quality is important to our business because we value our customers. We strive to provide our customers with constructions and services which meet and even exceed their expectations.
Maintaining customer satisfaction at the forefront and utmost level through our high-quality products with superior features forms the basis of our quality policy. The objective of our policy is to continuously follow innovations in this field and continue our improvement in terms of both technology and product quality, adopt a strong team effort in accordance with the legal requirements.
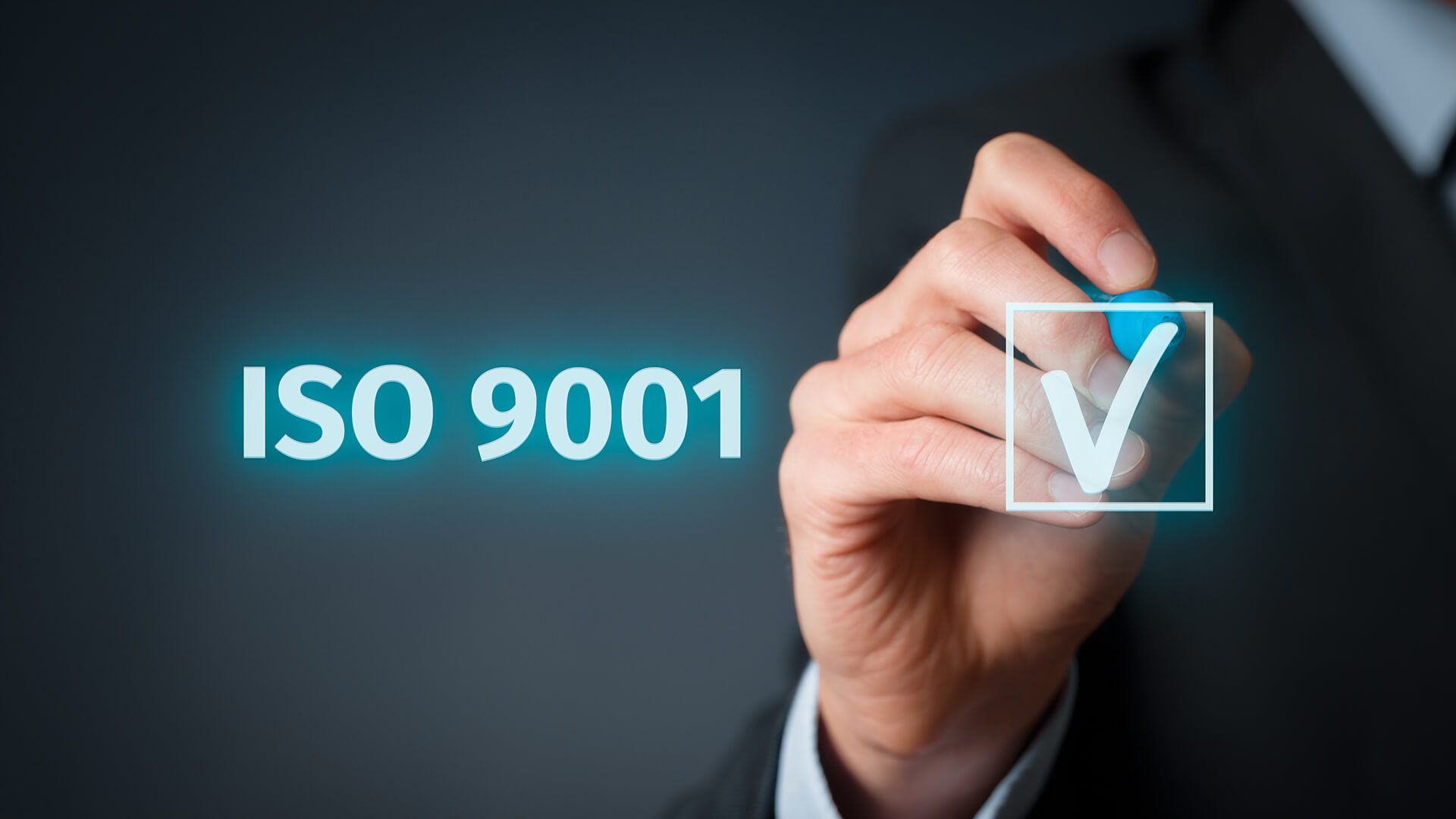
MTC is committed to:
• Continuous improvement and have established a Quality Management System which provides a framework for measuring and improving our performance.
• Providing customers with high-quality installations and services which meet requirements and are fit for their purpose.
• Enhancing the skills of management and staff through review and actively pursuing an on-going training policy, the objective of which is to prepare staff to perform their work more effectively.
• Promoting the culture of continual quality improvements and the philosophy of getting things “right first time”. • Rigorously controlling the supply, installation, and completion of the program of all projects.
• Promoting the quality management systems and ensuring implementation is achieved by internal auditing, management review, corrective and preventive action.
• Everyone is responsible for the quality within the company and for maintaining standards.
We have the following systems and procedures in place to support us in our aim of total customer satisfaction and continuous improvement throughout our business:-
• Regular gathering and monitoring of customer feedback.
• A customer complaints procedure.
• Selection and performance monitoring of suppliers against set criteria
• Training and development for our employees.
• Regular audit of our internal processes.
• Measurable quality objectives which reflect our business aims.
• Management reviews of audit results, customer feedback and complaints
Our internal procedures are reviewed regularly and are held in a Quality Manual which is made available to all employees. This policy is posted on the Company Notice Board and can also be found in the staff handbook. Though the General Manager has ultimate responsibility for Quality all employees have a responsibility within their own areas of work so helping to ensure that Quality is embedded within the whole of the company.
Name: KAMAL MOHAMED HAROON
Position: GENERAL MANAGER
Signature : Revision dated : 17-11-2020
1.3 Quality System
1.3.1 MTC. shall adopt the Quality Management System based on ISO 9001:2008.
1.3.2 This project shall be implemented and executed by M/s MTC under the Quality System Procedures, Method Statements, the Inspection and Test Plan, and various Checklists which are applicable to project efficient implementation with compliance to CLIENT requirements.
1.4 Preparation and Distribution of Project Quality Plan
1.4.1 This CLIENT has been prepared in compliance with CLIENT Quality requirements for this project and also in accordance with M/s MTC Quality Management system for quality delivery to the project quality specification and control.
1.4.2 This CLIENT shall be distributed to all key personnel on this project through the project Document Control Procedure.
1.4.3 This CLIENT shall be a live document for the whole duration of this project and where required, New Method Statement, ITP, and Checklists shall be prepared to satisfy the project requirements.
1.4 Preparation and Distribution of Project Quality Plan
1.4.1 This CLIENT has been prepared in compliance with CLIENT Quality requirements for this project and also in accordance with M/s MTC Quality Management system for quality delivery to the project quality specification and control.
1.4.2 This CLIENT shall be distributed to all key personnel on this project through the project Document Control Procedure.
1.4.3 This CLIENT shall be a live document for the whole duration of this project and where required, New Method Statement, ITP, and Checklists shall be prepared to satisfy the project requirements.
1.5 Quality Objectives
1.5.1 The work shall be performed throughout the execution period in accordance with the applicable Project Specification and Specification listed in the Contract Document, Approved for construction Drawings, Contract Requirements, National/International Codes and Standards, Contractor Quality System Procedure, Method Statement, ITP & Checklists.
1.5.2 To provide products and services for the realization of a successful project that meets the contract and project requirements to the satisfaction of the Employer.
1.5.3 To meet all quality requirements and technical performance criteria for the project.
1.5.4 To meet all commercial performance criteria, namely schedule and cost of efficient utilization of technology, human and material resources.
1.5.5 The National / International Codes and Standards, Quality Management System Procedures, Method Statement, ITP, and Checklists shall be controlled in accordance with the contract Quality System Procedure for Document Control.
1.6 Purpose
The purpose of this Quality Assurance Plan is to 1. Document the project Management System outlining its policies, objectives and defines those processes required for the management of the project.
2. Clearly define and document Project System Procedures, responsibilities, and accountabilities for managing project processes.
3. Assure the maintenance of adequate quality throughout all applicable areas of Contract performance.
4. Provide a mode of operation that emphasizes the identification, correction, and prevention of deficiencies and discrepancies.
5. Provide personnel with quality objectives to be achieved.
6. Consolidate the project management system to ensure the ongoing effectiveness of its functional operations despite employee movement and process change.
7. Provide a documented reference against which the System can be audited and the quality performance may be measured in order to identify opportunities for improvement of the system operated.
8. To provide a living document for the whole duration of the project and where required endeavor to go extra lengths in fulfillment of this project.
9. Finally, the purpose of this quality plan is to comply with CLIENT Quality Requirement right from the inception of the project to the completion and commissioning.
1.7 Definitions
Process – Result of process. The end item result of the meeting of all contract terms and conditions. Quality Records – Documentation of those activities wherein records of said activities must be maintained will be specified in the procedure or work instruction level documents, as applicable Procedure: Specified way to carry out an activity or a process
1.7.1 Owner CLIENT/CONSULTANT
1.7.2 Client CLIENT/CONSULTANT
1.7.3 Contractor MTC Trading & Contracting Co. WLL
1.7.4 OM Operations Manager
1.7.5 QMS: Quality Management System
1.7.6 QMSD: QMS Document
1.7.7 CLIENT: Project Quality Procedure
1.7.8. ME Material Engineer
1.7.9 PE Project Engineer
1.7.10 QCE QA/QC Engineer
1.7.11 QAP: Quality Assurance Plan
1.7.12 ITP: Inspection and Test Plan
1.7.13 NCR: Non-Conformance Report
1.7.14 MS: Method Statement
1.7.15 SI: Safety Inspector
1.7.16 QC: Quality Control
1.7.17 HSE: HSE Officer
1.7.18 CS: Chief Surveyor
Section 2 – Overall Project Management System
2.1 Project Organization & Responsibilities:
The Organization structure M/s MTC intends to utilize on this project consists of a team of competent, highly motivated, schedule-driven, and qualified personnel. The nominated person will be assigned full-time to the task force as the work developed. Project Organization Chart & Responsibilities attached – Appendix 4.
2.2 Project Communication:
The Project Manager is responsible for establishing and maintaining a communication system for this project in accordance with the requirements outlined in the relevant Contract Documents. Such system shall include communication with CLIENT project managers and all Subcontractors and suppliers appointed by the Management, with respect to the following items:
• Flow of Information
• Materials submittals
• Drawing submittals
• Weekly Progress Meeting
• Monthly Progress Meeting
• Inquiries and order handling, including amendments.
• Customer complaints and other reports relating to nonconformities
• Customer responses relating to the conformity of product and or I or service.
2.3 Project Procedure:
2.3.1 Objectives
The objectives of the Quality System Procedure is to describe the extent of detail required for adequate control of various Management System activities, the responsibilities, authorities, and verified works affecting Quality, how different activities are to be performed, the document to be issued and the control to be applied for the effective operation of the Quality Management System to achieve the quality objective of this project.
2.3.2 Quality Management System
The following quality assurance procedures will be implemented at every construction phase
if needs required.
1. Quality Manual MTC- QM-01
2. Management MTC -MR-02
3. Contract Review MTC -CR-03
4. Document Control MTC -DOC-04
5. Purchasing MTC -PUR-05
6. Subcontractor Work MTC-SUBCON-06
7. Store MTC-STO-07
8. Inspection and Test Plan MTC-INS-08
9. Control of Insp. Measuring & Testing Equipment MTC-CAL-09
10. Control of Non-Conformance MTC-CNC-10
11. Preventive Action Report MTC-PAR-11
12. Corrective Action Report MTC-CAR-12
13. Control of Quality Records MTC-CQR-13
Section3 – Document & Data Control
3.1 General
The Management defines a Project document management system, including relevant forms,
records needed to maintain an effective and efficient operation of a good Project Management
System and Documentation Process in accordance to CLIENT Engineering standard & QCS
This Quality Plan is a Project-specific document and includes:
• Statement of a quality policy, approved by the Project Management
• The Project Organization Chart – See attached App – 4.
• Job Descriptions of key staff at the site along with the specific allocation of duties and
responsibilities.
• Procedures which shall be applicable to the Project–See attached App – 5
• Inspection and Test Plans – See attached App – 6
• Forms, Records which shall be used by the Project App – 7
• Responsibilities
The plan will incorporate Engineering Procurement, Construction and all other relevant
activities required by the Contract.
3.2 Document and Data Control
3.2.1 For the purpose of this project, M/s MTC shall comply with all project specifications
in matters related to documentation and data control process by initiating
procedural control of the project as per CLIENT & Project Specific requirements for
quick and timely delivery and distribution of required documents to the concern
project personnel at an appreciable high level to meet with project specification in
accordance with basic document control requirements.
The Documents and Data Control Process cover the following activities:
a) Documents Numbering System Control
b) Control of Incoming & outgoing Correspondence
c) Control of Engineering Documents
d) Control of Technical Submittals
e) Control of Quality Documents
The project Document Controller is responsible for performing the above activities ensuring
compliance with the requirements of Project Quality Procedure for Management of
Documents.
QA/QC Engineer is overall in charge of the document and data control.
3.2 Document and Data Control
3.2.1 For the purpose of this project, M/s MTC shall comply with all project specifications
in matters related to documentation and data control process by initiating
procedural control of the project as per CLIENT & Project Specific requirements for
quick and timely delivery and distribution of required documents to the concern
project personnel at an appreciable high level to meet with project specification in
accordance with basic document control requirements.
The Documents and Data Control Process cover the following activities:
a) Documents Numbering System Control
b) Control of Incoming & outgoing Correspondence
c) Control of Engineering Documents
d) Control of Technical Submittals
e) Control of Quality Documents
The project Document Controller is responsible for performing the above activities ensuring
compliance with the requirements of Project Quality Procedure for Management of
Documents.
QA/QC Engineer is overall in charge of the document and data control.